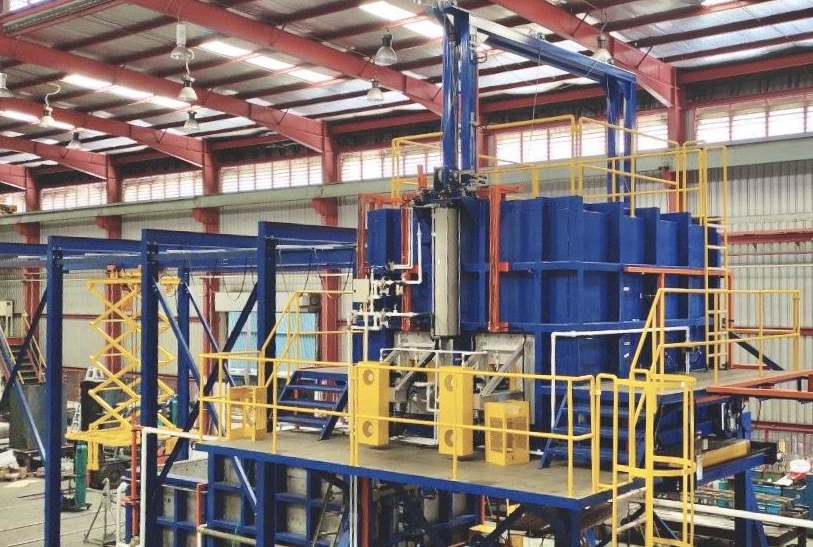
For applications requiring higher processing temperatures, industrial furnaces are often the best option. Industrial ovens can generate heat that cannot be obtained from external structures, and ovens are closed devices so that they generate and retain heat more efficiently.
In industrial furnaces, fuel and oxygen are mixed to generate heat, which results in combustion. The heat generated by the combustion process is released from the furnace in the form of flue gas. This type of heater typically reaches temperatures above 400 ° C (750 ° F). For applications requiring extreme heat, such as metal forming and heat treatment, industrial furnaces may be the right solution. The reasons are as follows:
- Industrial furnaces can offer unmatched functionality in the metal industry.
Efficient pouring, shaping and shaping of heavy metals requires strong and constant heat. Industrial ovens can reach temperatures that many other systems cannot. These high temperatures allow the metallurgical industry to perform demanding applications. These applications require intense uniform heat that can only be provided by an industrial furnace
With the right combination of combustion and high performance design, industrial furnaces can serve the metallurgical industry effectively and efficiently.
- The temperature range can be set according to the heating demand.
Depending on the temperature required to complete the application, industrial furnaces can be designed to meet specific requirements. When buying an industrial oven, it is important to know the temperature you will most often need to obtain an oven. This will allow you to choose the right oven that will withstand the required temperature in the long run.
For example, if 95% of applications require temperatures between 1000 and 1000, manufacturers can customize cost-effective furnaces to suit their heating needs. However, purchasing a 1000 ° F oven and using it only for applications with temperatures of 500 ° F can create temperature uniformity and process management issues.
- Each style of oven has its advantages.
Industrial furnaces are available in a variety of shapes and sizes, including box furnaces and tube designs. Each style is useful for a variety of reasons. For example, box furnaces are great for loading materials, and tube systems are generally better suited for continuous applications that occur in process tubes.
The versatile industrial oven also allows you to customize features such as door position, door type, load unit, and split interior options. This customizable option allows users to customize the device to meet the needs of their application.
For more information on industrial furnaces, click here to get in touch with GSE – one of the top engineering companies around!