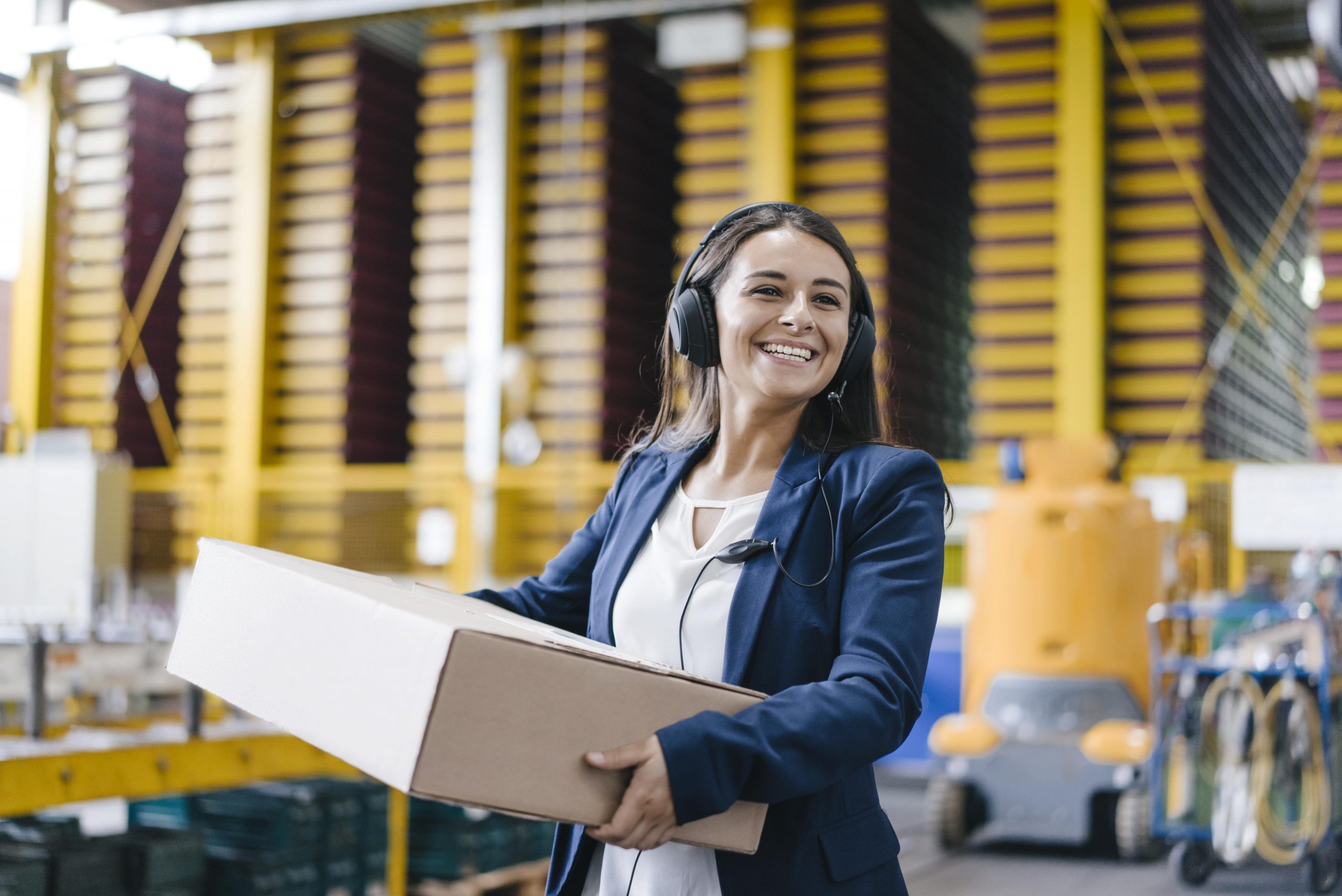
Managing warehouse operations and inventory may be challenging for a company owner in Malaysia. The good news is that these procedures can now more easily be automated and streamlined thanks to technology. Yet selecting the best system for your company may be challenging, particularly when you must decide between an inventory management system and a warehouse management system. We’ll explain the distinctions between the two in this post and assist you in choosing which is best for your company.
What is an Inventory Management System?
Managing warehouse operations and inventory may be challenging for a company owner in Malaysia. The great news is that these procedures can now more easily be automated and streamlined thanks to technology. Yet selecting the best system for your company may be challenging, particularly when you must decide between an inventory management system and a warehouse management system. We’ll explain the distinctions between the two in this post and assist you in identifying which is best for your company.
What is a Warehouse Management System?
A warehouse management system, on the other hand, is a software solution that helps businesses manage their warehouse operations. This system is designed to optimize the movement and storage of inventory within the warehouse. With a warehouse management system, you can track inventory levels, pick and pack orders more efficiently, and optimize your warehouse layout to improve productivity and reduce labor costs.
Key Differences between Inventory Management and Warehouse Management Systems
It is the emphasis of each system that most distinguish it from the other. In contrast to a warehouse management system, whose primary function is to oversee storage facility operations, an inventory management system tracks stock levels. Some significant distinctions exist, however:
- Inventory management systems may be simpler to deploy and operate since they are often less sophisticated than warehouse management systems.
- Inventory management systems are made for companies with lesser inventory requirements, while warehouse management systems are made for companies with bigger and more complicated warehouse operations.
- Systems for inventory management are often less costly than those for warehouse management.
Which System is Right for Your Business?
Which solution is best for your company now that you are aware of the distinctions between inventory management and warehouse management systems? The following variables influence the answer:
The size of your company:
If you run a little company with straightforward inventory requirements, an inventory management system can be enough. A warehouse management system could be required if your company is bigger and your warehouse operations are more complicated.
Your industry:
Various sectors have distinct requirements for inventory and warehouse management. For instance, a retail company could need more sophisticated inventory management tools than a manufacturer.
Your budget:
As warehouse management systems are often more costly than inventory management systems, it is important to take this into account while choosing.
Conclusion
Selecting the proper system for managing your inventory and warehouse operation is essential to the success of your organisation. Whether you go for an inventory management system or a warehouse management system, you will be able to simplify operations, decrease expenses, and increase productivity. By knowing the differences between these two systems and taking into account the specific requirements of your Malaysian business, you will be able to make an educated choice and choose the most appropriate system for your company.