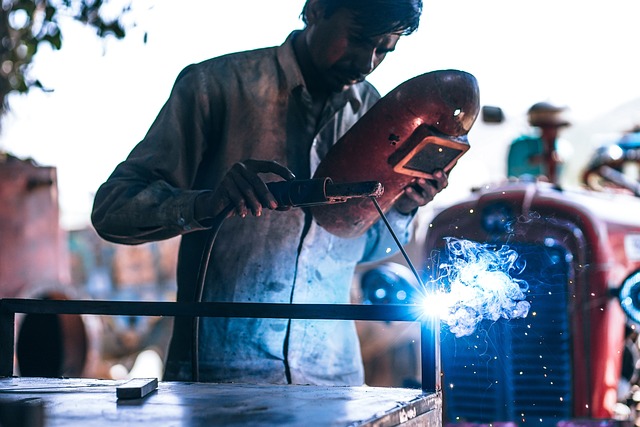
In the world of metal fabrication, efficiency and precision are paramount. To meet the demands of modern industry, professionals rely on cutting-edge equipment such as arc welders, plasma CNC cutting machines, and stainless steel welding machines. These tools have revolutionised how metal is manipulated, allowing for greater accuracy, speed, and overall quality in the fabrication process.
Arc Welders: Igniting Precision and Strength
Arc welding has stood the test of time as a reliable method for joining metals. Arc welders utilise electricity to create an intense heat that melts the base metals, fusing them when they cool down. This method offers a strong and durable bond, making it well-suited for construction, automotive, and aerospace applications.
One of the critical advantages of arc welding lies in its versatility. From manual metal arc (MMA) welding to gas metal arc welding (GMAW) and flux-cored arc welding (FCAW), different variations of arc welding cater to various metal types and fabrication requirements. This adaptability ensures that arc welders are indispensable tools across multiple metalworking tasks.
Plasma CNC Cutting Machines: Precision Redefined
When cutting intricate shapes and designs from metal sheets, plasma CNC cutting machines take centre stage. These automated systems utilise a high-velocity ionised gas (plasma) jet to cut through various metals precisely. Industries that demand intricate and accurate cuts, such as art, architecture, and industrial design, benefit immensely from the capabilities of plasma CNC cutting machines.
Combining computer numerical control (CNC) technology and plasma cutting reduces material waste and higher production efficiency. Operators can program these machines to follow complex patterns and designs, resulting in consistently precise cuts. Whether stainless steel, aluminium, or other metals, plasma CNC cutting machines ensure a streamlined fabrication process, reducing time and costs.
Stainless Steel Welding Machines: A Fusion of Strength and Corrosion Resistance
Stainless steel, renowned for its durability and resistance to corrosion, requires specialised welding techniques to maintain its integrity. Stainless steel welding machines offer tailored solutions to join stainless steel components effectively while preserving their unique properties. These machines employ techniques such as Tungsten Inert Gas (TIG) welding, which provides a controlled environment to prevent oxidation during welding.
The advantages of stainless steel welding machines extend beyond their ability to create strong joints. They ensure that the welded areas remain corrosion-resistant, making them ideal for applications in the food industry, medical equipment manufacturing, and architectural projects. This unique strength and corrosion resistance combination positions stainless steel welding machines as indispensable assets in metal fabrication.
Conclusion
In the dynamic world of metal fabrication, staying ahead requires embracing cutting-edge technologies. Arc welders, plasma CNC cutting machines, and stainless steel welding machines have emerged as transformative tools that enhance efficiency, precision, and quality in the fabrication process. These machines cater to diverse needs, from joining metals with strength and durability to cutting intricate designs with unmatched precision. Moreover, the specialised capabilities of stainless steel welding machines ensure that corrosion-resistant materials like stainless steel can be effectively integrated into various applications.
The demand for streamlined and advanced metal fabrication solutions will persist as industries evolve. Professionals can elevate their capabilities and deliver exceptional results in an increasingly competitive landscape by harnessing the power of arc welders, plasma CNC cutting machines, and stainless steel welding machines. Embracing these technologies isn’t just a choice; it’s a strategic move towards achieving excellence in metal fabrication.