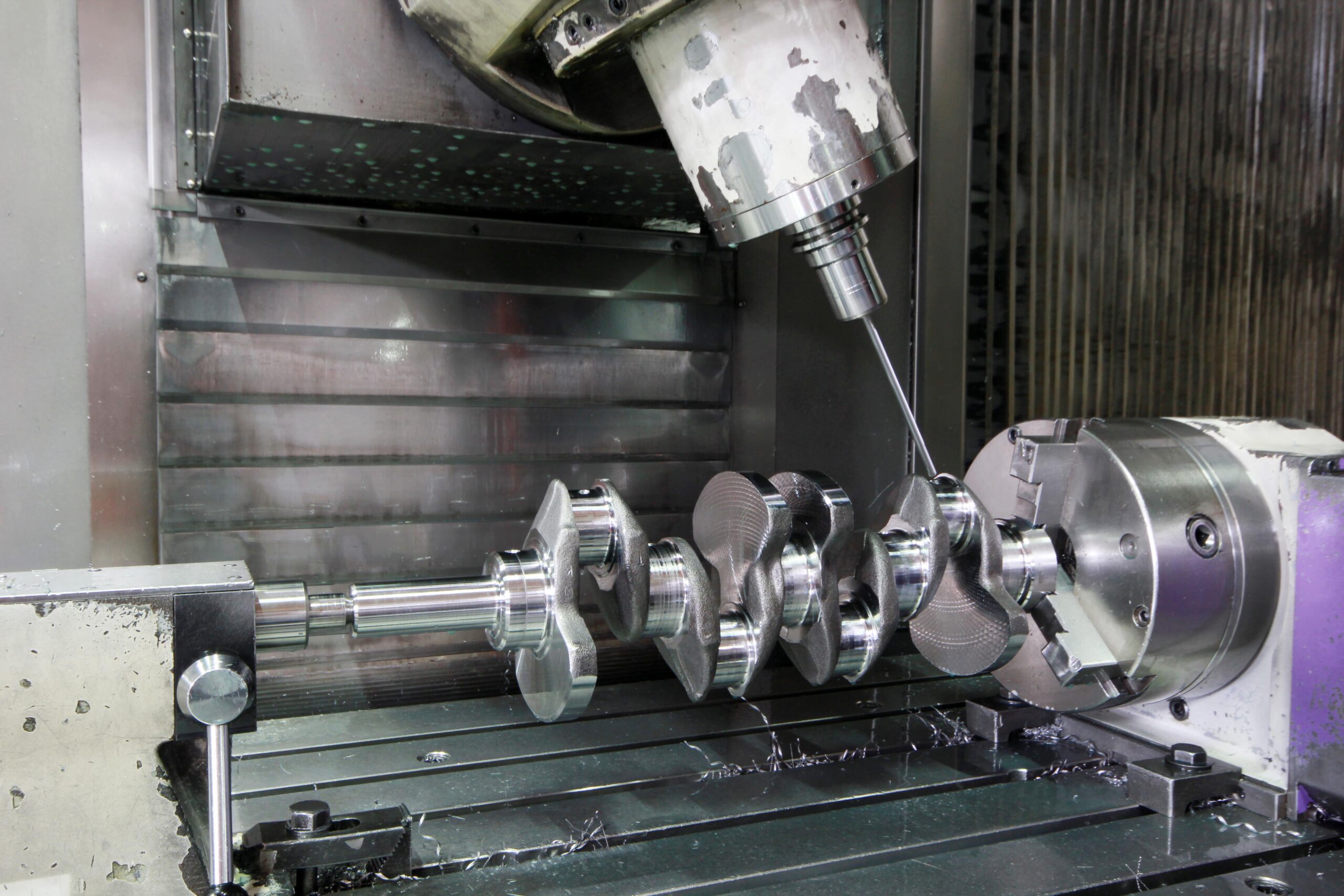
In the world of manufacturing, precision is key. Whether it’s in the creation of intricate components for aerospace technology or everyday consumer goods, achieving accuracy and consistency in the manufacturing process is paramount. This is where precision die castings and the aluminium die cast process shine. In this article, we will delve into the fascinating world of aluminium die casting, explore its different aspects, and understand the significance of aluminum casting impregnation. So, fasten your seatbelts as we embark on a journey through the world of precision and perfection in die-casting.
-
What is Die Casting?
Prior to discussing precision die castings, let’s define die casting. Die casting is a manufacturing process in which molten metal is injected into a steel mould, known as a die, in order to produce metal components with high precision and consistent quality. The mould is designed with the precise dimensions and shape of the desired element.
-
The Precision Die Castings Process
Understanding the Basics
Die-casting precision involves the production of intricate metal components. It’s similar to emptying liquid metal into a perfectly crafted ice cube receptacle, except the resulting ice crystals are incredibly intricate and tailored to your exact specifications.
The Role of Pressure
Pressure is a crucial element in this process. The use of pressure ensures that the molten metal occupies every crevice of the mould. This yields flawlessly precise and detailed components.
-
Crafting Excellence: Aluminium Die Casting Parts
Die-cast aluminium components are known for their lightweight and durability. From automotive components to electronic enclosures, die-cast aluminium components are utilised in a variety of industries.
The unique combination of Light Yet Mighty Aluminium’s high strength and low weight makes it an ideal material for manufacturing parts that must be both durable and simple to handle.
-
The Intricacies of the Aluminium Die Casting Process
Aluminium is melted and then injected into a die during the process of die casting. This results in components that are not only lightweight but also extremely resilient.
Efficiency Is Crucial
This process is exceptionally efficient. Die-casting technology has advanced to the point where intricate components can be manufactured at a rapid rate.
-
Strengthening Aluminum Castings: Aluminum Casting Impregnation
Aluminium casting impregnation is a vital phase in assuring the structural integrity of cast aluminium components. Sealing any porosity or microporosity in the castings by filling these cavities with a sealant using vacuum and pressure.
Enhanced Durability
This process increases the durability and strength of aluminium castings, making them suitable for even the most rigorous applications.
-
The Beauty of Aluminum Casting Parts
Indisputable is the adaptability of aluminium casting components. Aluminium die castings have everything, from intricate designs in automotive components to elegant finishes in consumer electronics.
Aesthetics and Performance
In design-conscious industries, they are favoured because they are both practical and aesthetically pleasing.
-
Benefits of Precision Die Castings
Unparalleled Precision
As the name implies, the primary advantage of precision die castings is their precision. The creation of parts with minimal post-processing reduces the requirement for additional machining.
Cost Effectiveness
Die casting is a cost-effective option due to its efficient material utilisation and reduced need for secondary processes.
-
Industries and Applications
Precision die castings are utilised in a variety of industries. Aerospace, automotive, electronics, and healthcare are among the main industries in which die cast elements play a significant role.
Aerospace: Strong and Light
In the aerospace industry, the lightweight and durable characteristics of die-cast aluminium parts make them a perfect fit for aircraft components.
Automotive: Driving Efficiency
The precision and cost-effectiveness of die-cast components in engines, transmissions, and structural elements are advantageous to the automotive industry.
Electronics: Precision at Its Best
Miniature and intricate elements are essential in the electronics industry, making precision die castings a top choice.
Healthcare: Reliability Matters
In the healthcare industry, where reliability and accuracy are of the utmost importance, die casting is a crucial component of medical devices and apparatus.
-
Quality Control in Die Casting
Die casting places a premium on the maintenance of quality. There are stringent quality control measures in place to guarantee that each component meets the necessary specifications.
Examination and Testing
To detect any defects, parts are subjected to thorough inspection and testing, including X-ray examination.
-
Environmental Considerations
In a world that is increasingly concerned with sustainability, die-casting has not been left behind. Continuous efforts are made to reduce the industry’s environmental footprint.
Recycling and Sustainability
In die casting, the recycling of waste metal and the use of eco-friendly materials are becoming commonplace.
Conclusion: A Glimpse into the Future
The world of die-casting is a constantly evolving one. As technology advances, so does the precision and efficiency of the process. The future holds exciting possibilities for die casting, with innovations in materials and design.